Solar cell modules work in the extremely harsh natural environment outdoors. Many materials (aluminum alloy frame, ultra-white glass, EVA, TPT, PVDF) used for assembly are new technologies or patented materials, regardless of the material itself or its surface treatment. The process has a high technical content.
Bonding and sealing of laminate and frame
The assembly requirements of the frame and the laminated laminate are tight fit and firm connection. There must be a good seal between the frame and the laminate. Although it is a close fit, it is required not to damage the glass. Assembling with press-fit sealing strip has the advantage of simple and quick assembly, but its bonding strength is not high. Relying on the elastic deformation of the rubber strip to fill the microscopic unevenness in the sealing gap, the deformation capacity of the rubber strip is limited, especially the small defects cannot be completely filled, resulting in low reliability of the seal. The advantages of assembling with adhesive are as follows:
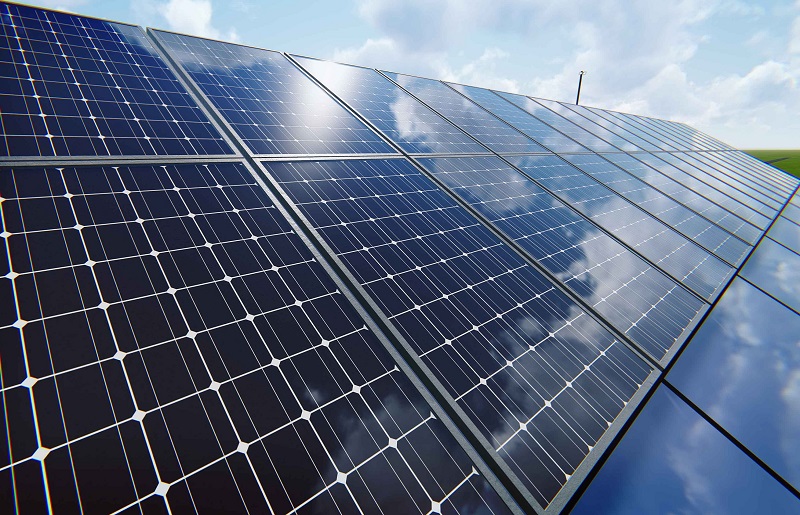
The liquid adhesive fully fills the sealing gap, and the microscopic unevenness on the surface can be well filled. After curing, an elastic adhesive layer is formed, and the sealing ability is significantly improved; the laminate and the frame are connected through the adhesive to achieve a continuous and high-strength connection, solar cell modules The bearing capacity and overall rigidity are greatly improved, and the stress distribution is more uniform; the cured adhesive layer has good elastic deformation ability to adapt to the thermal deformation and external force deformation in the use of solar cell modules.
Because the solar cell modules work in the extremely harsh natural environment outdoors, many materials (aluminum alloy frame, ultra-white glass, EVA, TPT, PVDF) used in their assembly are new technologies or patented materials, regardless of the material itself or its surface The treatment process has a high technical content. There are also big differences between the materials supplied by different manufacturers. We have done a lot of comparative experiments and studies on all kinds of materials used in solar cell modules (anything in contact with adhesives or indirect effects). The following aspects need to be paid attention to when selecting material suppliers and formulating assembly processes:
(A) Surface treatment process of aluminum alloy frame and bonding performance of adhesive
Aluminum or aluminum alloy itself has poor oxidation and corrosion resistance, but after proper surface treatment, it exhibits excellent oxidation and corrosion resistance. The surface of the aluminum alloy frame used for assembly of components has been processed by a certain process, and the commonly used processing processes include anodizing, electrophoretic coating, and fluorocarbon coating. 1527 solar cell module special sealant, anodized aluminum alloy surface, and acrylic electrophoretic coating aluminum alloy surface have good bonding performance and aging resistance.
(B) Bonding of backplane material and adhesive
TPT has almost become synonymous with backsheets. In 2007, the production capacity of the entire solar cell module industry increased sharply, and the contradiction between the demand and supply of backsheet materials was prominent. When TPT was not available, many manufacturers tried new backsheets such as PET and PVDF. Board material. Whether the adhesive and the backplane polymer materials are bonded or not has a lot to do with the molecular structure and surface energy of the backplane material. If the surface of the backplane material is not treated in any way, its surface energy is very low, and the bonding strength is very low. The surface of these backplane materials can only be bonded after proper surface treatment. Surface treatment methods of this type of polymer materials include corona treatment, plasma treatment, flame treatment and primer treatment.
Cell and glass, backplane packaging
The cells cannot generate electricity stably for a long time without being packaged. As a power source, a number of single cells must be connected in series and in parallel and tightly sealed into components. The glass, cell, and backplane materials need to be encapsulated by adhesives. This layer of adhesive must not only provide good electrical insulation properties, but also have the following characteristics: high light transmittance; UV stability (non-yellowing); certain Elasticity, so that the cell will not be broken under thermal deformation and external impact.
The most widely used packaging material is EVA. EVA is a kind of hot-melt adhesive, which undergoes fusion bonding, cross-linking and solidification under certain conditions of hot pressing, and becomes a high light-transmitting material. The cured EVA can withstand temperature changes and is elastic. The battery sheet, the upper glass and the lower back plate are bonded together by vacuum lamination technology using EVA. With the development of photovoltaic building integration technology, the encapsulation process of EVA materials has exposed certain limitations, especially for some special-shaped double-glass solar cell modules, it is difficult to encapsulate by common lamination process. UV-curable adhesives can use wet potting process, no need to pressurize and heat, only need a certain wavelength and intensity of UV light irradiation for tens of seconds to be fully cured, meeting the requirements of packaging, this technology is expected to become a future development direction.

Photovoltaic module junction box bonding
After the solar cell module is packaged, it is necessary to bond the junction box and the backplane together with an adhesive. This requires the adhesive to have good bonding properties to various backplanes and junction boxes. In order to ensure that the junction box will not fall off the backplane even after long-term aging under the condition of local stress, the adhesive is required to have good tear resistance and aging resistance.
Potting of junction box of photovoltaic module
The insulation performance requirements of the components in the junction box are very high. Under abnormal working conditions, a large amount of current will flow through the bypass diode and heat the solar cell module. In order to improve the heat dissipation performance and insulation performance of the junction box, it is necessary to use potting glue, and To achieve the effect of moisture-proof and earthquake-proof. The potting glue should have the following characteristics: good fluidity, able to flow into small gaps; a certain operating time and faster gel time; good insulation performance after curing; no corrosion to the bus bar; Good aging resistance. Two-component silicone potting glue has good insulation properties, thermal conductivity and aging resistance, non-corrosive and has good fluidity, and has been widely used in the potting of junction boxes.
The sealing between the bus bar and the cutout of the back plate
Photovoltaic module junction box potting glue, in order to prevent external moisture from penetrating into the solar cell module from the cut of the bus bar backplane, it needs to be sealed with an adhesive. Adhesives should have good insulating properties and have certain requirements for viscosity. Low-viscosity adhesives are not thick enough to achieve the sealing effect; high viscosity cannot well infiltrate the bus bar, which affects the sealing performance.